Folding with the Profimach Multilateral bending-Center makes your dreams come true!
The Profimach Multibend-Center panel bender is available in working lengths of 1000mm, 1500mm, 2000mm, 2500 mm
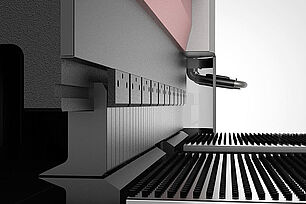
Automatic Panel Bending Machine
More affordable than you think
In recent years, in the field of sheet metal processing, the application of automated processing technology has gradually become popular. The core technology of sheet metal processing automation lies in the automation of sheet metal bending. In the traditional bending method, when processing large-size and heavier parts, usually multiple operators are required to complete it, which is labor-intensive and the working environment is harsh. Therefore, fully automatic bending centers came into being and gradually began to replace manual bending.
The automatic panel bender is an automatic equipment for processing thin metal plates below 3mm. Its structure mainly includes a tool holder, worktable, a clamping feeding device and a CNC operating table. The worktable is composed of a base and a clamping piece feeding structure. The workpiece is positioned and clamped on the worktable and delivered to the processing position through the feeding mechanism, and the bending tool is driven by the tool holder to process the workpiece.
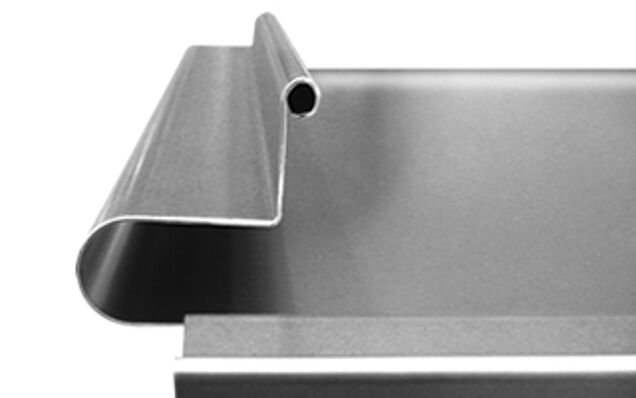
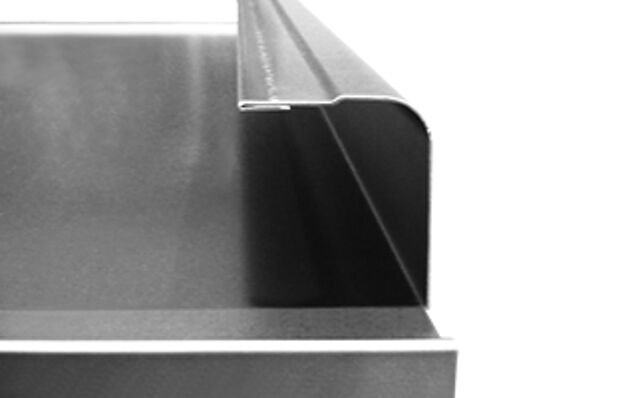
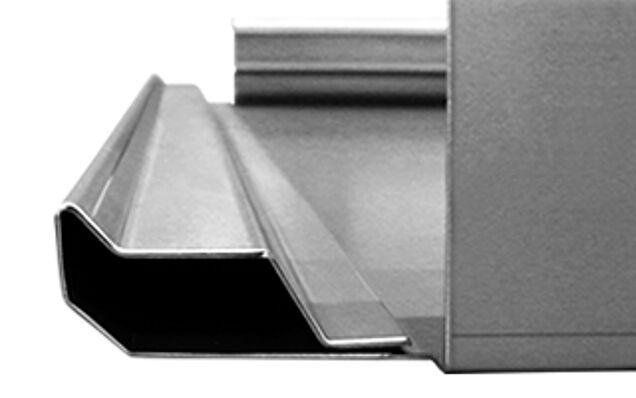
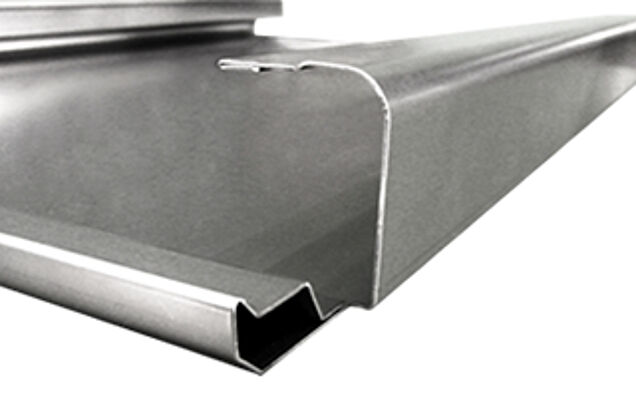
Servo electrical fully-automatic panel bending machine
The intelligent CNC automatic panel bending machine/press brake machine is an equipment for processing thin plates. Its structure mainly includes a tool holder, worktable, aclamping feeding device and a CNC operating table. The worktable is composed of a base and a clamping piece feeding structure. The workpiece is positioned and clamped on the worktable and delivered to the processing position through the feeding mechanism, and the bending tool is driven by the tool holder to process the workpiece.
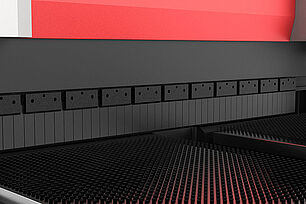
The Limitations of Traditional Sheet Bending Machine
1. High Labor Cost
In the traditional bending method, at least three auxiliary workers and one skilled worker are required to bend large galvanized sheets with a thickness of 1.2mm. For the bending of small plates, a skilled worker must rest for 20 minutes, and the accuracy of each bending is different. At the same time, the tacit understanding of the operators is insufficient, which is very easy to cause work injuries.
2. Poor Product Consistency
In traditional bending methods, for special processes such as arc processing, on the one hand, in the actual bending process, limited by the experience level of the bending workers, the error of arc bending is relatively large. On the other hand, the consistency of each bent sample is poor, which brings difficulties to later welding.
3. Low Efficiency
In the traditional bending method, the bending machine needs to prepare different bending molds according to different bending angles such as right angles, acute angles, arcs, etc. Workers need to frequently replace molds during actual operation, resulting in low work efficiency. At the same time, in the bending process, due to the direct contact bending, the damage to the abrasive tool is relatively large. Once the mold is damaged, the bending accuracy will be seriously reduced.
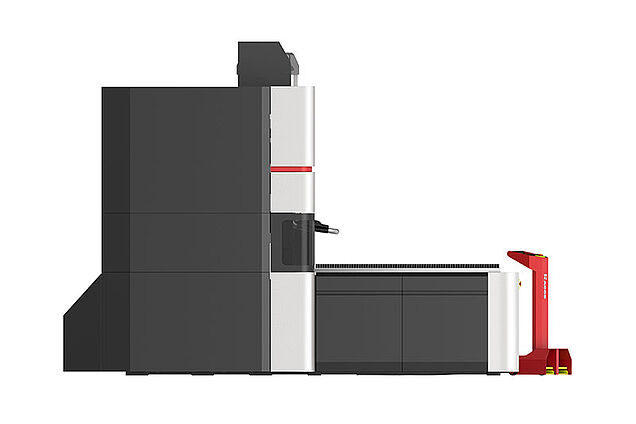
The Advantages of Automatic Panel Bending Center
The fully automatic panel bending center independently developed by profimach will change the traditional bending method. It has the advantages of high precision, high efficiency, low cost, and high safety..
1. High Accuracy of Automatic Sheet Bending Machine
On the one hand, the automatic sheet bending machine adopts a servo clamping method to ensure the stability of feeding and improve the processing accuracy of the product. On the other hand, unlike the previous staff holding the sheet to bend, automatic sheet bending machine uses a mechanical arm to bend the sheet without error, thus ensuring the quality of batch processed products.
2.High Efficiency of Automatic Metal Sheet Bending Machine
In the manual bending process, workers need to lift large plates throughout the entire process. Once the operations are not synchronized, errors will occur, resulting in low efficiency. However, the automatic bending center does not need to manually lift the plate, avoiding the error caused by manual operation asynchronously, and improving the production efficiency. At the same time, the fully automatic bending center is equipped with universal molds, which eliminates the need to frequently replace upper and lower molds during the bending process, saving a lot of manpower and improving efficiency. In addition, through fully automatic positioning, the fully automatic bending center can achieve high-efficiency bending efficiency of 0.2s/cut continuous bending.
3. High Security and Easy Operation of Automatic Panel Bender
Compared with the traditional bending method, the fully automatic bending center does not need to lift the plate in the whole process, avoiding the staff from being injured due to improper operation, and the whole bending process is safer. At the same time, the fully automatic bending center is equipped with a variety of intelligent programs, and the staff can operate without professional skills.